قبل از مطالعه کامل مقاله در مورد مشکلات پوششهای ضدخوردگی بخوانید:
خلاصه ای از مهمترین نکات موجود در این مقاله
- تحقیقات نشان میدهد که مشکلات رایج در پوششهای ضد خوردگی شامل ترکخوردگی، پوسته شدن و ایجاد حبابهای هوا است که هرکدام دلایل و روشهای پیشگیری خاص خود را دارند.
- ترکخوردگی معمولاً به دلیل انقباض پوشش یا اجرای نادرست رخ میدهد، درحالیکه پوسته شدن اغلب ناشی از چسبندگی ضعیف و آمادهسازی نامناسب سطح است.
- حبابهای هوا معمولاً به دلیل رطوبت محبوس شده یا دمای بالای زمان اجرا ایجاد میشوند و پیشگیری از آن مستلزم کنترل صحیح شرایط محیطی است.
- در صنایع پتروشیمی، پوششهای لولهها با چالشهای اضافی مانند خوردگی حفرهای و شیاری مواجه هستند که نیاز به سیستمهای پوششی ویژه دارند.
مقدمه
پوششهای ضد خوردگی نقش حیاتی در حفاظت از تجهیزات صنایع پتروشیمی و پالایشگاهی دارند. خوردگی میتواند منجر به آسیبهای پرهزینه و خطرات ایمنی شود. بااینحال، مشکلاتی مانند ترکخوردگی، پوسته شدن و ایجاد حباب در پوششها میتوانند عملکرد آنها را مختل کنند. این مقاله به بررسی این مشکلات، علل ایجاد آنها و روشهای پیشگیری از آنها میپردازد و بر نیازهای خاص صنایع تاکید دارد.
- پیشنهاد مطالعه بیشتر:
- پوشش ضد خوردگی: معرفی جدیدترین تکنولوژیها و مزایای استفاده
- کاربرد پوششهای ضدخوردگی در صنایع دریایی و سکوهای نفتی: مبارزه با خوردگی در محیطهای شور و مرطوب
مشکلات پوششهای ضدخوردگی
پوششهای ضد خوردگی ممکن است به دلیل انقباض یا ضخامت بیشازحد دچار ترک شوند، در صورت چسبندگی ضعیف از سطح جدا شوند و در صورت وجود رطوبت یا گرمای زیاد، حباب بزنند. هر یک از این مشکلات راهکارهای پیشگیری خاصی دارند، مانند آمادهسازی صحیح سطح و اجرای پوششها در شرایط مناسب.
ملاحظات صنعتی
در محیطهای پتروشیمی، لولهها بهطور ویژه در معرض خوردگی حفرهای و شیاری هستند. استفاده از سیستمهای پوششی باکیفیت و روشهایی مانند حفاظت کاتدی میتواند به کاهش این خطرات و افزایش دوام پوشش کمک کند.
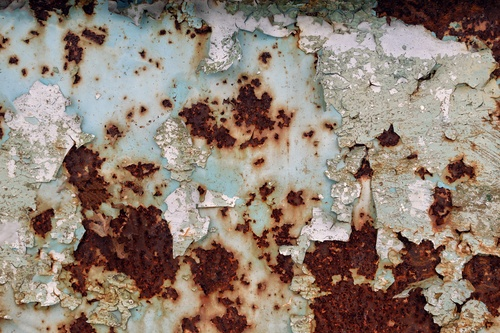
تحلیل مشکلات پوششها و روشهای پیشگیری
اهمیت موضوع
در صنایع پتروشیمی و پالایشگاهی، خوردگی یک تهدید جدی برای طول عمر تجهیزات و ایمنی عملیاتی محسوب میشود و خسارات مالی قابلتوجهی به دنبال دارد. پوششهای حفاظتی بهعنوان یک مانع مؤثر، از سطوح فلزی در برابر عوامل خورنده مانند اکسیژن و رطوبت محافظت میکنند. بااینحال، این پوششها ممکن است دچار ترکخوردگی، پوسته شدن و ایجاد حباب شوند که عملکرد آنها را تضعیف میکند. این مقاله به بررسی مشکلات پوششهای ضدخوردگی، علل آنها و استراتژیهای پیشگیری پرداخته و به ملاحظات خاص صنعتی و استانداردهای مرتبط اشاره میکند.
مشکلات رایج در پوششهای ضدخوردگی
1. مشکلات ناشی از فرآیند اعمال پوشش
- پوشش ناهموار: ضخامت غیر یکنواخت پوشش میتواند منجر به نقاط ضعیف در برابر خوردگی شود. این مشکل اغلب به دلیل استفاده نادرست از ابزارهای اعمال یا عدم کنترل مناسب فرآیند رخ میدهد1و3.
- ایجاد حباب (Blistering): ورود هوا یا رطوبت به لایه پوشش باعث ایجاد حبابهایی میشود که با ترکیدن آنها، فلز زیرین در معرض خوردگی قرار میگیرد1و8.
- چکیدن مواد پوششی (Dripping): تجمع مواد اضافی روی سطح، علاوه بر تأثیر منفی بر ظاهر، ممکن است باعث کاهش چسبندگی شود1.
2. آمادهسازی نامناسب سطح
عدم تمیزکاری کامل سطح قبل از اعمال پوشش یکی از دلایل اصلی خرابی زودهنگام است. آلودگیهایی مانند روغن، گرد و غبار یا زنگزدگی میتوانند چسبندگی پوشش را کاهش داده و منجر به پوسته شدن یا جدا شدن آن شوند5و8.
3. مشکلات محیطی و شرایط نامناسب اجرا
- دما و رطوبت بالا یا پایین میتوانند فرآیند خشک شدن و پخت پوشش را مختل کنند. این مسئله باعث کاهش مقاومت مکانیکی و شیمیایی پوشش میشود3و8.
- باد یا جریان هوا ممکن است ذرات رنگ را به مناطق غیر هدف منتقل کرده و منجر به ایجاد لایههای نازک و ضعیف شود3.
4. انتخاب نادرست مواد پوششی
استفاده از موادی که با شرایط محیطی سازگار نیستند، مانند انتخاب پوششهای غیرمقاوم در برابر مواد شیمیایی خاص یا دماهای بالا، میتواند عملکرد سیستم را تضعیف کند2و7.
بررسی دقیق تر مشکلات پوششهای ضدخوردگی
- ترکخوردگی
- توضیح: ترکها باعث ایجاد شکافهای عمیق در پوشش میشوند که میتوانند فلز زیرین را در معرض خوردگی قرار دهند.
- دلایل: انقباض پوشش، انعطافپذیری محدود، ضخامت بیشازحد یا اجرای پوشش در دمای بالا از دلایل اصلی ترکخوردگی هستند.
- روشهای پیشگیری: آمادهسازی صحیح سطح، اجرای پوشش در ضخامت توصیهشده و کنترل شرایط محیطی در زمان اجرا و خشک شدن پوشش از جمله راهکارهای جلوگیری از ترکخوردگی هستند (Industrial Coatings: Defects, Causes, and Solutions).
- پوسته شدن
- توضیح: در این حالت، پوشش بهصورت ورقههایی از سطح جدا میشود و فلز را بدون محافظت باقی میگذارد.
- دلایل: چسبندگی ضعیف ناشی از آمادهسازی نامناسب سطح، انتخاب نادرست سیستم پوششی یا تنشهای مکانیکی بالا از مهمترین عوامل این مشکل هستند.
- روشهای پیشگیری: انتخاب پوشش مناسب، تمیزکاری دقیق سطح و استفاده از استانداردهای بینالمللی مانند ISO 12944 برای بهبود چسبندگی ضروری است (IMIA-WGP-126-22-Coating-Failures.pdf).
- حبابهای هوا (تاولزدگی و تشکیل حباب)
- توضیح: این مشکل بهصورت برجستگیهای کوچک یا بزرگ در سطح پوشش دیده میشود و میتواند چسبندگی پوشش را مختل کند.
- دلایل: عوامل ایجادکننده این مشکل شامل آلودگیهای نمکی، حلالهای محبوس، دمای بالا یا رطوبت زیاد هستند.
- روشهای پیشگیری: حذف آلایندهها از سطح، کنترل دمای محیط و استفاده از پوششهای مناسب برای بسترهای متخلخل (Common Causes of Blistering and Bubbling in Industrial Coatings).
استانداردها و الزامات داخلی مشکلات پوششهای ضدخوردگی
در صنعت پتروشیمی ایران، استانداردهایی مانند IPS و NACE اهمیت ویژهای دارند. استاندارد IPS بر اساس استانداردهای بینالمللی مانند ISO و API تنظیمشده و در پروژههای نفت و گاز اعمال میشود (استاندارد IPS). همچنین، تحقیقات نشان داده که پوششهای پلیاورتان با درصد جامد بالا، مقاومت به خوردگی مناسبی دارند و برای محیطهای خورنده توصیه میشوند (بررسی محافظت از لوله های انتقال نفت و گاز در مقابل خوردگی با استفاده از پوشش های پلی اورتان).
نتیجهگیری
مشکلاتی مانند ترکخوردگی، پوسته شدن و ایجاد حباب در پوششها میتوانند ریسکهای جدی برای تجهیزات صنایع پتروشیمی و پالایشگاهی ایجاد کنند. بااینحال، با اجرای راهکارهای پیشگیری مؤثر، رعایت استانداردها و استفاده از سیستمهای حفاظتی مدرن، میتوان این مشکلات را به حداقل رساند. ادغام راهکارهای صنعتی مانند پوششهای پیشرفته و حفاظت کاتدی میتواند مقاومت به خوردگی را بهبود بخشیده و از بروز خرابیهای زودهنگام جلوگیری کند.
منابع و مراجع
- https://www.lksteelpipe.com/info/3-major-problems-of-anti-corrosion-coating-mat-99484556.html
- https://comunemetaltech.com/addressing-key-challenges-in-anti-corrosion-protection-for-thermal-systems-and-refineries/
- https://www.linkedin.com/pulse/why-do-anti-corrosive-coatings-fail-prematurely-demech-chemical
- https://latem.com/blog/prevent-corrosion-metal-parts
- https://www.sealxpert.com/surface-preparations-for-an-affective-anti-corrosion-coating
- https://vivablast.com/new/3-methods-anti-corrosion-contractor/
- https://eoncoat.com/corrosion-prevention-methods/
- https://www.ipspaint.co.uk/industrial-paints/overcoming-challenges-in-industrial-protective-coatings-ips-paint-supplies/
- Common Causes of Blistering and Bubbling in Industrial Coatings
- Industrial Coatings: Defects, Causes, and Solutions
- Understanding Pipeline Corrosion Prevention and the Best… | Polyguard
- IMIA-WGP-126-22-Coating-Failures.pdf
- بررسی محافظت از لوله های انتقال نفت و گاز در مقابل خوردگی با استفاده از پوشش های پلی اورتان
- API 970 , استاندارد کنترل خوردگی فلزات | پارس اکتان
- استاندارد IPS